If you consider fluid systems, proper flow must be accomplished, along with backflow prevention, two of the most essential criteria to ensure efficient and safe processes. Vacuum breakers and check valves are the most critical components for performing the two most important work.
Although both devices are meant to control the flow of fluids, they work on different principles and are used in various applications. This article will go in-depth about checking valves and vacuum breakers, and by the end, you’ll find the two crucial system parts that differ from each other so that you can choose which one meets your requirements.
What is a Check Valve?
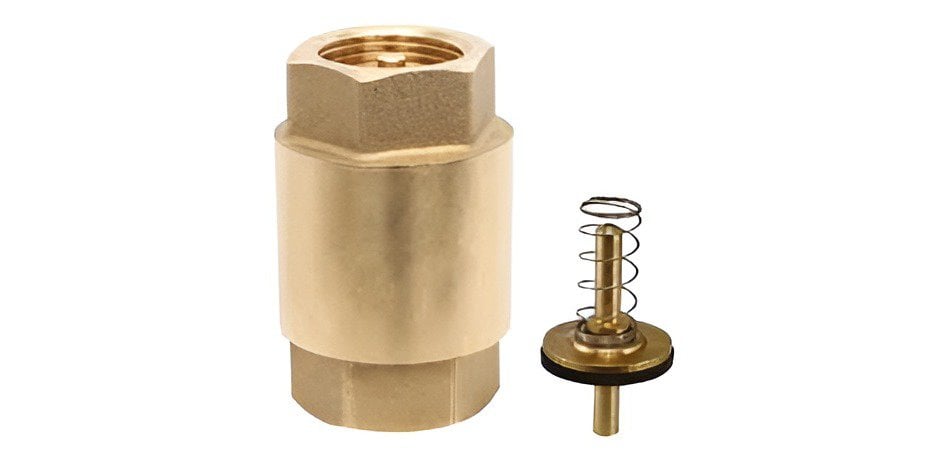
A check valve, called a non-return valve, is a valve that permits fluid, either liquid or gas, to move in only one direction and prevent backflow. This component of many systems, along with fluid backflow, may lead to damage or a loss of efficiency.
Check valves work automatically and require no manual manipulation. They consist of a valve body, a disc or ball, and a spring. When flowing in the intended direction, the fluid pushes the disc or ball off the seat, allowing the fluid to pass through. On stoppage or reversal of the flow, the spring or backflow force pushes the disc or ball onto the seat to seal the valve against backflow.
Check Valve Types
Swing Check Valve
A swing check valve has a disk that turns to let the flow go through or shut off. With flow, the disk swings open, allowing fluid to pass through. When the flow stops, it turns back to shut to prevent reverse flow.
This makes them perfect for applications where backflow prevention is essential. However, they may be less effective in high-velocity systems since they will cause water hammer.
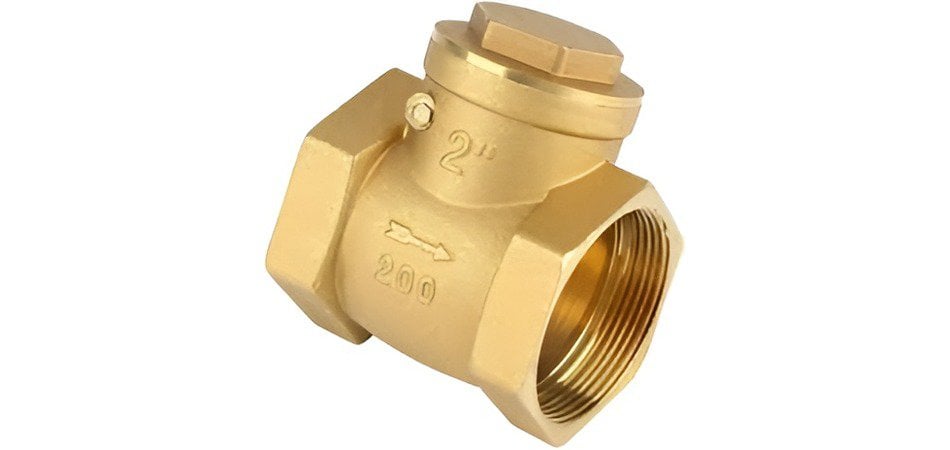
Lift Check Valve
Lift check valves control the flow using a disk that goes up and down. Fluid movement causes the disk to lift, allowing the fluid to pass. Reversed flow makes the disk fall back into position, blocking reversed flow. These valves perform well under high-pressure applications.
Due to the moving parts, they need more servicing than swing check valves and are less ideal for systems with fluctuating flow rates.
Ball Check Valves
Ball check valves feature a moving ball that either closes or opens flow. The ball is seated, pushed off its seat by the pressure of the incoming flow, and then returns to stop backflow when flow reverses. They are reliable and rugged, functioning well in high and low-flow conditions. The internal design, however, can make cleaning and maintenance quite tricky.
Spring Check Valve
Spring-loaded check valves are structures with a spring that holds a disc or ball. The spring will compress and allow flow once pressure is applied, but in the lack of flow, it applies force on the disk or ball back on the seat, thereby blocking the reverse flow.
This makes them useful in applications where a fast response to changes in flow is essential. The only problem with the spring is that it is undergoing continuous moving, which makes it wear out with time.
Check out our blog on Spring Vs. Check Valve; Difference Between Them
What is a Vacuum Breaker?
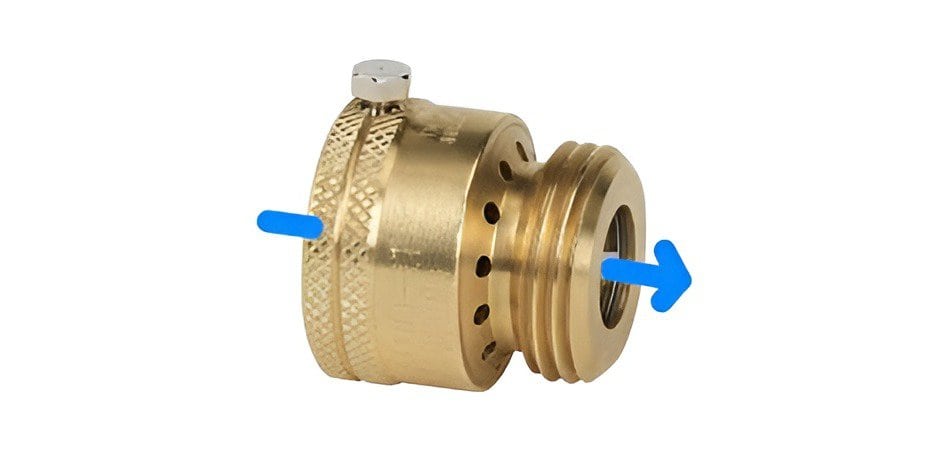
A vacuum breaker is a type of mechanical device that stops back-siphonage. It means an unwanted reverse flow of water or other fluid into the potable water supply system due to creating a vacuum or negative pressure.
Back-siphonage can occur under many varied circumstances, for example, suddenly in the central water supply pressure, and may cause contamination of a potable water system.
The operation of a vacuum breaker is based on a particular type of valve mechanism that is set to open by default in case a vacuum is detected and the air is sucked into the system. The airflow halts the vacuum, preventing the reverse flow of contaminated water into the potable water supply.
Read our complete blog on: What is Vacuum Breaker?
Types of Vacuum breaker
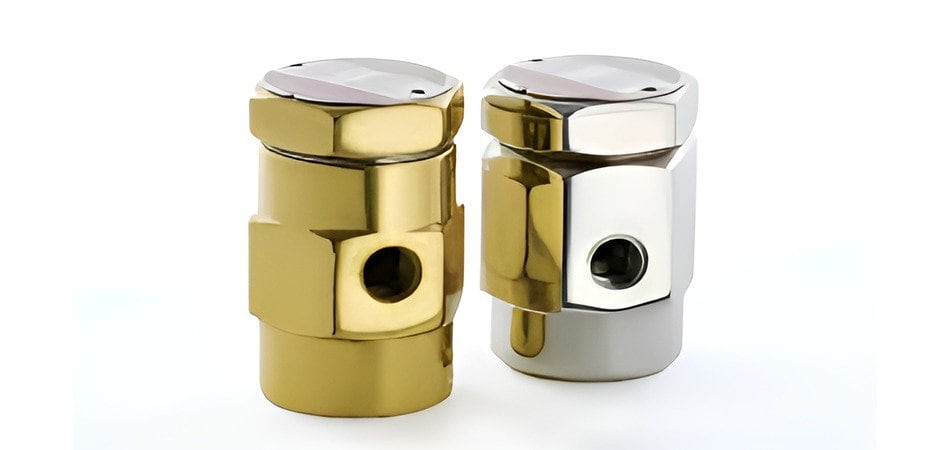
Atmospheric Vacuum Breaker
This simple, low-cost-to-install mechanism prevents sewage from siphoning into a plumbing system. It allows air into the system if a vacuum or negative pressure is present. The system avoids siphoning polluted water back into the clean water supply.
This is often installed on irrigation systems. Mounting it above the highest point of a system ensures that the AVB is always operational. While it is effective and, due to the nature of its operation, self-cleaning, it would be unsuitable in systems under constant pressure or where the backflow conditions may be extreme.
Pressure Vacuum Breaker (PVB)
The pressure vacuum breaker shall stop both back-siphonage and backpressure. This device combines a pressure relief valve with a vacuum breaker. The pressure relief valve maintains a constant pressure but allows the release of unsafe pressures while the vacuum breaker stops the creation of a vacuum that might bring about contamination. This type of PVB has a spring-loaded check valve that opens when a vacuum forms to let air into the system.
It is commonly used in irrigation systems and, more precisely, in areas where a backpressure is likely to occur. Of course, it won’t work correctly if its elements aren’t serviced accordingly; it has to be tested and certified occasionally.
Hose Bibb Vacuum Breaker
Hose Bibb vacuum breakers are designed to attach to hose bibbs or outdoor faucets. They prevent water from backflowing due to pressure loss within the water supply line or when a vacuum occurs. They are easy to install and quite common as a device used on residential systems to avoid contamination via garden hoses.
Inline Vacuum Breaker
Inline vacuum breakers incorporate themselves directly into the piping without standing out as separate fittings inside the system. While opening to admit air into the system and sensing the vacuum, it resists backflow at this point. These are used where the space is challenged, and ease of installation is a consideration.
Double Check Valve Assembly DCVA
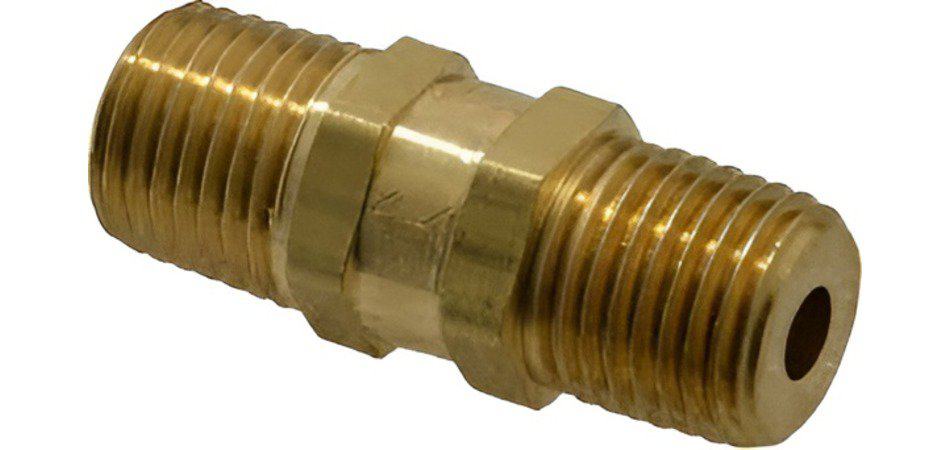
The double check valve assembles two check valves in series. Each valve is meant to stop backflow by closing should water try to flow the other way. A DCVA is appreciably more protective than any check valve as it is double functioning.
It can be used under moderate risk of contamination, as may be industrial and commercial uses. This assembly should be tested regularly to verify that both check valves are correctly seated and to avoid cross-contamination.
Check Valve Vs. Vacuum Breaker: Major Differences
A check valve and a vacuum breaker are significantly different in design, operation, and applications, although both are for preventing undesirable backflow.
Material Difference:
Check valves let the flow in one direction but block it in the other through a pipeline. Often, check valves are fabricated with materials that offer them strength, such as brass, stainless steel, or plastic.
The reasons for using brass and stainless steel are these materials’ anti-corrosion and strength characteristics, respectively, and their high pressure and temperature resistivity support the application of check valves in high-pressure and high-temperature systems. In low-pressure systems, plastic check valves resist chemical corrosion, but not in extreme conditions.
Vacuum breakers, on the other hand, prevent the creation of a vacuum that could siphon contaminated water into a clean water supply. They are often fabricated from plastics, brass, or composite materials.
Plastics are used as they are not corrosive and are relatively inexpensive. Brass is chosen for increased strength and pressure capabilities, while composite materials offer medium strength and resistance in varying environmental conditions.
Size Difference
Check Valve(Swing) Size
Size |
H |
L |
¼” |
39.0 |
55.0 |
3/8″ |
39.0 |
55.0 |
1/2″ |
39.0 |
55.0 |
¾” |
43.0 |
63.0 |
1″ |
48.0 |
73.0 |
1 ¼” |
58.0 |
81.0 |
1 ½” |
61.0 |
92.0 |
2″ |
68.0 |
108.0 |
2 ½” |
86.0 |
137.0 |
3″ |
97.0 |
148.0 |
4 |
113.0 |
180.0 |
Vacuum Breaker Standard Size
Size (Inches) |
Flow Rate (GPM) |
Connection Type |
½ |
Up to 15 |
Threaded, Solder |
¾ |
Up to 25 |
Threaded, Solder |
1 |
Up to 40 |
Threaded, Solder, Flanged |
1 ¼ |
Up to 60 |
Threaded, Flanged |
1 ½ |
Up to 90 |
Threaded, Flanged |
2 |
Up to 150 |
Flanged |
3 |
Up to 300 |
Flanged |
Principle of Operation:
The critical operational difference between a check valve and a vacuum breaker is that while a check valve allows fluid passage in one direction and has a mechanism of closing the backflow, such as a disc, ball, or others, automatically, a vacuum breaker admits air into the system by sensing a vacuum condition and thus prevents back-siphonage.
Check valves are versatile and will find their way into industries that need to prevent backflow in their fluid systems, be they liquids, gases, or steam. On the contrary, vacuum breakers are designed only for potable water systems and find specific use in preventing contamination due to back-siphonages.
Generally, check valves are found in plumbing, irrigation systems, and a few industrial applications where water should be kept pure.
Design and Components:
Depending on the design, check valves are broadly categorized into swing check valves, lift check valves, ball check valves, and diaphragm check valves, each with some components that make one design better for specific applications. There are two significant types of vacuum breakers: atmospheric vacuum breakers and pressure vacuum breakers.
AVBs have a simple design and operate by the action of atmospheric pressure, whereas PVBs have an integrated check valve in the makeup for use at much higher pressures.
Cost and Complexity:
Check valves are generally less complex and cheaper than vacuum breakers. Vacuum breakers, particularly pressure vacuum breakers, are more complex and expensive because they have an integrated check valve, and their installation and maintenance requirements are much more accurate.
Which One is Better?
Vacuum preventer
A check valve is likely the better solution for preventing backflow in liquids, gases, or steam-running applications. Check valves are versatile, inexpensive, and relatively easy to install and maintain. They work well in systems that need to prevent backflow for safety and efficiency.
On the other hand, if you are dealing with potable water systems and your principal concern is to stop a back-siphonage to protect against contaminating the water, a vacuum breaker would be the better choice.
Vacuum breakers comprise several parts designed to maintain the water supply by preventing the backward flow of contaminated water into the system. They are more complex, requiring proper installation and maintenance, but specific applications would find them an indispensable part, given their protective function for the public’s health.
Conclusion
Check valves and vacuum breakers are two of the most vital accessories for fluid systems; these ensure proper fluid flow and the preclusion of reverse flow. Understanding their differences and applications should give you an edge over which one to use to fulfill your requirements. Whether you choose a check valve for its general versatility and easy operation or a vacuum breaker for its functionality in protecting water purity, having the right one is crucial to the safety and effectiveness of your system.