What is a Butterfly Valve?
A kind of valve that is a quarter-turn rotary motion employed to stop, regulate, and start the flow. The term “butterfly” in a butterfly valve is a disk connected to a rod. A 90° rotation of the handle can fully close or open the valve. Butterfly valves are famous in the industry because they are lightweight, fast operation, and low-cost. These valves employ handles, gears, or automatic actuators as required. In this blog, you will study the different types of valves.
What are the Butterfly Valve Parts?

The butterfly valve has only four primary parts: the body, the disk, the stem, and the seat.
Butterfly valve body:
Butterfly valves typically have bodies that nestle between two pipe flanges, with lug and wafer body designs being the most common.
Butterfly valve disk:
This disk is equivalent to a ball in the ball valve, a plug in a plug valve that prevents flow. Various disk designs and orientations exist to optimize flow, sealing, and/or operating torque.
Butterfly valve Stem:
The stem of a butterfly valve may be a one-piece shaft or a divided stem. The stem is covered from the media in the most resilient seated structure, permitting an economical material selection regarding cost and mechanical properties.
Butterfly valve Seat:
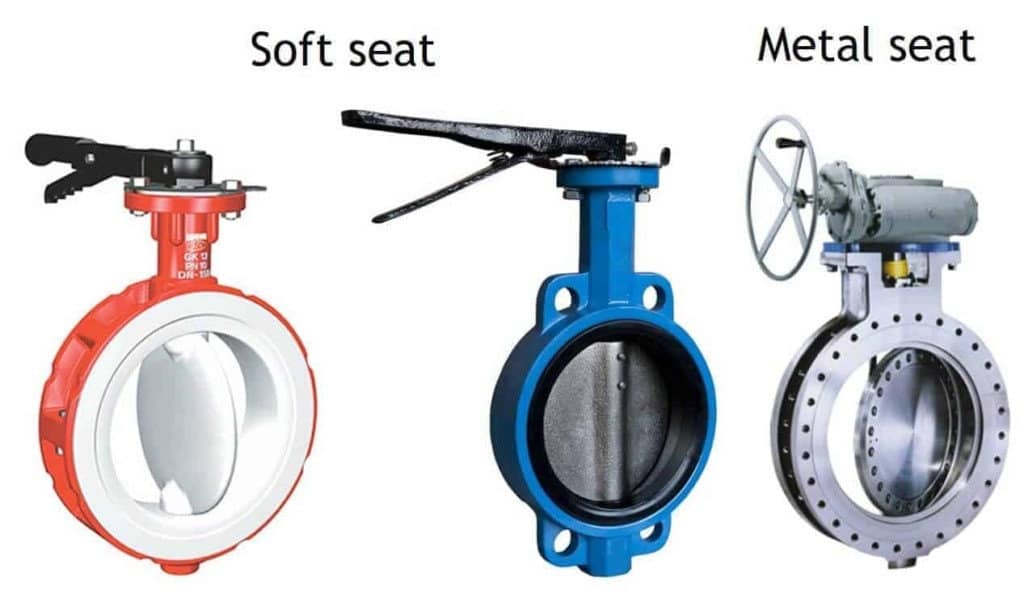
An interference fit among the disk edge and the seat accomplishes the closure of a resilient-seat butterfly valve. Numerous elastomers and polymers can be used to construct a seat. The seat may be linked to the body, pressed, or secured into place.
Butterfly valve: working principle
The fluid flow is controlled by rotating the valve disc in a butterfly valve, whose structure is relatively simple. In the closed position, the disc obstructs the valve bore. The open position is perpendicular to the flow direction to permit passage.
Typically, butterfly valves allow for bidirectional flow and shutoff. Yet, as they are not full-bore, they cannot be employed for pigging or swabbing. The body’s internal and external surface areas are coated with an epoxy particle coating. Depending on the technical specifications and application-specific requirements, the valves are typically operated by handwheels, gears, actuators, or a combination thereof.
Butterfly Valve Size
Size (mm) | Size (Inch) | L |
40 | 1 ½ | 41 |
52 | 2 | 43 |
65 | 2 ½ | 46 |
80 | 3 | 46 |
100 | 4 | 52 |
125 | 5 | 56 |
150 | 6 | 56 |
200 | 8 | 60 |
250 | 10 | 68 |
Types of Butterfly Valve Based on Piping Connection
- Lug-style butterfly valve
- Wafer-style butterfly valve
- Flanged butterfly valve
- Butt-welded butterfly valve
Here, we will discuss only the lug-style and wafer-style butterfly valve
Lug-Style Vs. Wafer Style Butterfly Valve: What is the Difference
1. Difference by Definition
What is the Wafer Butterfly Valve?
In wafer valves, butterfly valves are positioned between two pipe flanges connected by long bolts across the valve’s body. There may or may not be flange openings on the exterior of the valve body. O-rings and gaskets mounted in a flat valve face are placed on both sides between the valve body and the pipe flange to obtain a strong seal.
Wafer butterfly valves have the most cost-effective connection design. Still, they cannot be used as isolation valves or at the termination of a line. The entire pipeline must be turned down when performing maintenance on either side of the wafer butterfly valve.
As with certain varieties of butterfly valves, wafer valves should not be used in high-temperature applications because the valve body will expand, resulting in increased stress on the bolts and possible failure.
What is Lug Butterfly Valve?
To install a lug butterfly valve, bolts are threaded through the lugs (threaded inserts) that protrude from the valve body and into the pipe flanges. Two bolts on either side of the valve hold it in place; no nuts are needed in either lug. The valve can then be used as an isolation valve or for end-of-line applications. The valve may be disassembled from one side without impacting the other, reducing maintenance downtime.
However, the weight of the pipeline is also passed to the valve body. Thus, the valve must bear a greater load. When a butterfly valve is positioned at the end of a line, its pressure rating typically decreases since no downstream flange keeps the seat in its intended position. The media must distort the seat to get beyond the disc and seat seal.
Generally, the pressure rating of lug-style butterfly valves used in dead-end service is lower. Lug-style valves, in contrast to wafer butterfly valves, support the piping’s load within the valve body.
- Lug style Vs. Wafer Style Butterfly Valve: Working
How does a lug-style butterfly valve work?
A butterfly valve with lugs is a quarter-turn valve. This indicates the valve disc rotates a quarter turn to turn on or close the fluid stream. To access a butterfly valve with lugs, the handle must be rotated 90 degrees counterclockwise for a quarter turn. The torque imparted to the handle through the valve stem is transmitted to the valve disc. This turning causes the valve’s disc to rotate and become parallel to the direction of fluid flow. This condition leaves the valve open, permitting fluid to pass through.
To halt the fluid flow, the handle is turned a quarter turn in the opposite direction (counterclockwise). This rotation causes the disc to become perpendicular to the flow of the fluid. The position of the disc perpendicular to the fluid stream ensures that the fluid flow path is obstructed, preventing any fluid from passing through the valve. Manufacturers of lug-type butterfly valves design this valve for shutoff and modulating applications. To restrict fluid flow, the handle is turned slightly to let the disc rotate and permit a small amount of fluid flow.
How Does the Wafer Style Butterfly Work?
Wafer butterfly valves function similarly to other quarter-turn valves. This valve comprises multiple components, with the metal disc being the most vital part. This metal disc is often referred to as the butterfly. When the valve is closed, the rod-mounted butterfly prevents liquid passage.
Once the valve opens, the metal disc or butterfly rotates a quarter-turn. The path is accessible and permits the unrestricted flow of liquids or air. How the valve is partially or completely opened or closed will determine how the disc travels.
If the valve is only partially open, the disc will not complete a quarter revolution and may not permit unobstructed passage. Therefore, small volumes of liquids or air will pass through. If the valve is fully opened, the disc will rotate 90 degrees, allowing greater fluid or air to pass through.
The butterfly wafer valve consists of numerous additional components. They include the body, the seal, the packaging, the stem, the actuator, and the resilient seat. The robust seat is set on the valve’s body to produce the ideal seal. If the sturdy seat is damaged, the packaging provides an additional seal.
Industrial butterfly valves are available in different configurations. Some methods are performed manually, while others are performed electronically. They also come in various styles, which can be obtained from an industrial valve supplier. Some offer exceptional efficacy in front suctions and a massive pump line.
- Lug style Vs. Butterfly Valve: Design Features

Wafer and lug valves come in many different shapes and sizes, each with unique features that make them suitable for various uses. Most wafer butterfly valves have simple designs with two discs joined by a shaft in the middle. On the other hand, lug butterfly valves normally have more than one part, such as discs, sleeves, nuts, and bolts.
Also, wafer butterfly valves generally have longer stems than lug-style valves, which gives them higher flow rates with less pressure drop. Also, some types have rubber or elastomer gaskets that make them better at sealing. These design features make wafer and lug butterfly valves very flexible parts that can be used in almost any pipe system.
- Lug style Vs. Wafer Style Butterfly Valve: Best Seat Material
The best seat material for lug-style and wafer butterfly valves depends on several factors, including the type of fluid being transported, the fluid’s temperature and pressure, and the valve’s operating conditions.
PTFE: Polytetrafluoroethylene (PTFE) is a fluoropolymer that is highly resistant to chemicals and can withstand various temperatures. It is commonly used for butterfly valve seats in highly corrosive or aggressive fluids applications.
EPDM: Ethylene propylene diene monomer is an artificial rubber commonly used for butterfly valve seats. It is known for its excellent resistance to water, steam, and mild acids and bases.
NBR: Nitrile butadiene rubber (NBR) is a synthetic rubber commonly used for butterfly valve seats in petroleum-based fluids applications. It has excellent resistance to oils and greases.
Viton: Viton is a fluoroelastomer that is highly resistant to chemicals and can resist high temperatures. It is commonly used for butterfly valve seats in highly corrosive or aggressive fluids applications.
- Lug style Vs. Wafer Style Butterfly Valve: Installations Mechanism
Installation of the wafer butterfly valve
The wafer butterfly valve must be put together in the following ways:
1. Put the wafer butterfly valve between the two special flanges for installed wafer butterfly valves. Ensure the bolt holes in the flanges align with the round holes in the butterfly valve body.
2. Put the bolts and nuts into the holes in the flange to connect the valve body to the flange. Ensure the method is flat, but don’t tighten the bolts and nuts too much.
3. Weld the plate to the pipe. This should be done by spot welding.
4. First, take off the wafer butterfly valve.
5. Weld the pipe’s two flanges together to finish the fixing.
Install the wafer butterfly valve after the weld between the flange and the pipe has cooled. Now, pay close attention to how much the butterfly plate is opened.
7. Move the butterfly valve back into place and tighten the nuts, but be careful not to tighten them too much.
8. Open the butterfly plate of the butterfly valve to ensure it can be opened and closed easily.
9. Cross the bolts again and tighten them evenly.
10. After doing all the above, test the butterfly valve again to ensure it can open and close easily.
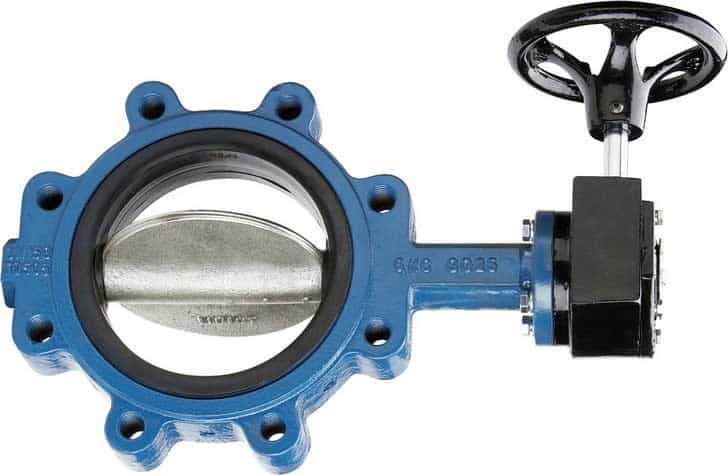
Lug-style butterfly valve installation
First, the level or handwheel must be installed depending on whether the device is manual or gear-dependent. Then, it would be best if you turned the lever clockwise to close it completely. You must align the disc so that its edges are parallel.
If you cannot correctly align the disc, try slightly loosening the top plate and then gradually turning the lever clockwise before retightening the top plate. If you are installing a valve that is actuated by a gear, you only need to tighten the nuts on the gearbox’s side.
Multiple times can be spent opening and closing the disc to ensure proper operation. Currently, you must install the valve into your existing piping system. You must determine whether you plan to install the lug-type butterfly valve horizontally or vertically. Installing the lug-type butterfly valve horizontally in the presence of check valves is often advantageous, as this prevents disc wear and ultimately increases the valve’s longevity. You must inspect the pipeline’s alignment beforehand.
It is improper to alter the alignment of the pipeline’s lug-type butterfly valve. In addition, the flange ends of the lug-type butterfly valve and the terminal flange ends of the pipeline should be completely inspected. This investigation is crucial because it ensures the valve and the pipeline are defect-free.
Unlike the wafer or angle globe valve, the lug-type butterfly valve must be installed between the flanges with small cap screws and the valve’s outlet and inlet. Then, cautiously insert the disc-equipped valve into the flange. Ensuring that the valve is snug and centered on the flange is essential.
After repairing the valve, it must be fully opened so that there is no obstruction to the disc’s movement. After the verification, the fasteners in the flange must be tightened in a crisscross or star pattern before they can be loaded. You must apply pressure to the pipe so that if there is a leak, it can be halted immediately and then tighten the bolts.
Important note:
The variety of piping in the building services industry uses lug fittings, so double-check your specs and installation to ensure that wafer-type fittings aren’t used at any places along the line that could eventually require maintenance or replacement. The double-flanged type should be considered for large-diameter uses.
- Lug style Vs. Wafer Style Butterfly Valve: Quality Assurance Standards
Before wafer and lug butterfly valves are used in any application, the quality assurance standards must be examined to ensure they are safe and work properly. These valves should be checked for damage on the outside before use. Also, checking for internal wear and rust is a good idea. Also, all valve parts should be checked for wear and tear or problems.
It is important to remember that all the fitted parts should meet the requirements, such as the maximum pressure and temperature. Lastly, manufacturers should provide documents that show they follow relevant safety standards. This will ensure that the product is safe and reliable.
- Lug style Vs. Wafer Style Butterfly Valve: Advantages

Wafer style butterfly valve: Advantages
• The flowing medium may travel through a stream-lined butterfly disc without experiencing an important reduction in pressure or limitation in flow.
• Butterfly wafer valves are quick-acting; transition the valve from the completely open to the fully closed position, and the stem must be rotated 90 degrees (1/4 turn).
• The butterfly wafer valve design is well-suited for flow regulation. It fails to produce an enormous turbulent flow when partially opened or closed.
• Butterfly wafer valves are more suitable for diverse uses because they are typically less expensive and lighter.
Lug style butterfly valve: Advantages
- Light is weight
- Bidirectional sealing
- Easy to install in any diagonal, vertical, or horizontal position
- Small-size butterfly valve
- Easy to maintain
- Replaceable body seat and low-pressure drop